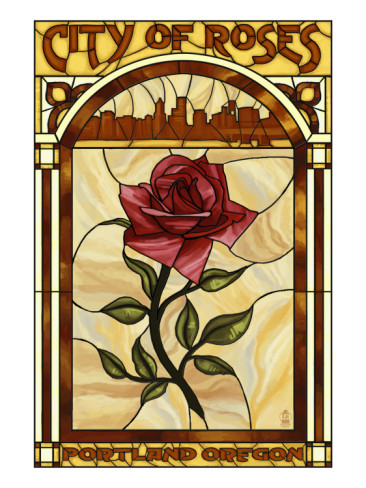
Between the twelfth and the fifteenth century, craftsmen created some of the most outstanding work in stained glass. Stained glass gave the medieval Church a compelling and dramatic way of communicating with the people through church and cathedral windows. But after this period, the directedness and richness of stained glass work began to be lost as the designs became too elaborate and were often just over-detailed copies of paintings. Today we are much more in sympathy with the style of the earlier craftsmen with its emphasis on strong simple shapes.
The techniques described in this hub are the basic ones needed for most forms of leaded stained glass work. A panel to hang in a window, or even a whole replacement windowpane, is probably the simplest piece of leaded stained glass work for a beginner, with reasonable standards of care and accuracy, to tackle.
Lampshades and lanterns, because of their more complicated structure require more skill. However, they still use the same basic processes that are described here and could soon be undertaken after practice.
How the Glass is Colored
Many people believe that the stained glass artist puts color on the glass. This is not so; color is incorporated into the glass as it is made. Glass is a combination of silica, soda, lime and oxides that are fused in a furnace with the mineral that produces the color. Cobalt makes blue, uranium or copper creates green, cadmium, copper or even gold will produce red. When the ingredients are melted, the glassblower gathers some on the end of a pipe and blows it into a cylindrical shape. This is then cut open and spread into a flat sheet. Because glass is made in this way there are varying thickness, bubbles, streaks and an infinite variety of color tones. This variety gives you great scope in your stained glass design and makes every piece of work unique.
Principles of Design
The first important point to remember when beginning to choose colored glass for a design of stained glass work is the way the quality of the color is changed enormously by the light that shines through. Remember, too, that the interior of a room, in much the same way as the interior of a cathedral, is basically dark and the contrast with bright daylight is therefore very strong. This contrast is made even greater by the darkness of the lead strips that outline and hold each section of glass. What this means in practice is that you should choose glass literally twice as dark as you initially think is right because the light shining through will tone the color down so much.
Different from Painting!
Forget the way you judge colors in painting. Color relationships in glass are very different. Light, surprisingly makes blue come forward and red recede. And these same colors, if placed together, do not stand out clearly from each other but both take on a purple tone. So experiment all the time, holding the glass up to the daylight to learn how to choose and combine colors for your designs.
Another obvious distinction between painting and glasswork is that, as glass is hard and has to be cut, it is always clearly distinguished from the next piece, there is no blurring or merging of colors as in painting.
It is useful to know the rules for heraldic design, made so that identification was easy at a distance on a battlefield, because they are often applied to glass design. Colors are placed next to metal and not next to each other. In glass terms, white and yellow are the silver and gold of heraldry and they are placed next to strong colors for contrast.
Strong Simple Shapes
Let’s say you are going to make a straightforward leaded glass panel. You will have bought a selection of glass from a stained glass workshop or craft store, both quarter sheets and mixed smaller pieces are available. Bear your selection of glass in mind and begin by making a full-sized color design sketch. Keep it simple, limit your colors, but use pieces in a variety of sizes. Remember the effect of the network of dark leading, which will be the strong designs lines in your panel.
Making the ‘Cutline’
When you are satisfied, trace the lines of the design carefully, including the outside edges. This tracing paper becomes your ‘cutline’ and all the glass is cut to fit it. The lines on the tracing should be about 1/16” thick. The cutline is then put down flat and the pieces of glass placed down on it in turn to be cut to size.
Cutting Technique
If you have not cut glass before, practice first. You will be able to buy the right kind of single wheel glasscutter and replacement wheels from your craft store. Hold the glasscutter upright, as shown in the figure on the right., placing it between the first and second fingers with the thumb supporting the hammer edge. Score the surface of the glass firmly in an even continuous line flowing along the edge of your tracing line. (The thickness of the line represents the middle of the lead.) Move either towards or away from you, whichever feels right, but do not go backwards and forwards on the same line or the break will not be clean and you will blunt the wheel. With the hammer side of the cutter tap along the score line on the back of the glass till it breaks. Snip off any rough pieces or slivers with pliers.
Color Testing
You will want to continue testing the colors against the light as you cut the pieces because you may decide to make adjustments. The best way to do this is to take a plain sheet of glass. Paint in black lines, 1/4” thick on the back following the exact pattern of the cutline. These painted lines will represent the whole width of the leads. Prop the glass up against the light and stick the glass pieces up in position as you cut them with blobs of modeling clay so that you can study the effect.
Painting on the Glass
This is the stage at which you can paint on to the glass pieces if you want that effect, and you have an enameling kiln. Painted shading or detail can emphasize design and modify the light that comes through the glass. The special stained glass paint comes in browns, grays and black, the intention is not to color. It is in powder form and you mix it with diluted gum Arabic, using a palette knife on a piece of ground glass. Paint on the glass sections with a soft brush; hold your work up to the light to judge the effect.
Firing in the Kiln
When dry put the pieces, with space between them, on a kiln shelf which has been covered with a smooth layer of dry plaster. Place in the kiln and bring the heat up slowly to about 9.752°F. The paint should then appear almost glossy. Turn the kiln off and leave the glass to cool.
The Leading Process
You are now ready to fit your glass together, rather like a jigsaw. Each piece is slotted into a lead strip, know professionally as a ‘came’. It comes in 1/2” and 1/4” sized and is H-shaped in construction so that glass fits in on both sides.
Lead is soft enough to be bent around the curves so that joints are only necessary at the angles and where new sections as added. (All these joints will eventually be soldered together.)
Prepare the Lead Cames
You must first prepare your lead came by stretching it before using it. Put one end into a vice and pull from the other end with pliers, you will feel the lead give. Then you have to open up each side of the lead so that it will take the thickness of the glass. Use either a special stopping knife for this or an old blunt kitchen one. You will also need a lead cutting knife, you can make your own if you wish from an old knife cut off short and sharpened across the blade so that it will cut downwards.
Work Systematically
Work on your leading on an old wooden board. The paper cutline should be placed on it under the glass as your guide. Start at one side with a lead and slot in the glass pieces, systematically moving across the design, cutting the lead where necessary. Tap the glass pieces into the lead as tightly as possible with the lead-weighted handle of the stopping knife or with a light hammer. You will find that it is helpful to use nails tapped into the wood, braced against the glass, to hold a piece temporarily in place until you are ready to cope with it by fixing it into the lead.
Soldering the Lead Together
When you have assembled the whole panel, you must solder the joints in the lead cames. Prepare each joint by cleaning thoroughly with a wire brush until it is bright, the surface must be absolutely clean if the soldering is to work. Then rub a little tallow on to the joint to act as flux.
Lead solder melts quite easily but you must nevertheless have a good soldering iron that gets hot enough for the lead and solder to fuse thoroughly. A gas soldering iron is satisfactory but the flame means that there is some risk to the glass. It is therefore best to use an electric iron of 80 watts with a 1/4" bit.
The copper bit must be prepared before you use it each time. File it clean. Then heat the iron and rub tallow on the bit as flux. Melt a little solder on it and rub it on an old tin can lid until the bit is coated smoothly all over.
You are now ready to solder the joints. Feed in a strip of solder on to the joint with one hand while you press down on it with the hot iron held in your other hand as shown in the picture. Press down until you have produced a melted puddle of lead, but use no more solder than is necessary. When you have finished all the soldering on the top surface, turn the whole panel over and repeat the process on the other side.
Grouting
Grouting is the last major process in leaded stained glass work. Putty is worked thoroughly into all the gaps in the lead on both sides. It serves two purposes, it weatherproofs the panel and it prevents it rattling. You can either use proprietary metal glazing putty, which you must darken with black powder color or you can make your own from these ingredients:
3 Parts Whiting
1 Part Plaster
Black Powder Color to Darken
Linseed Oil to Bind
Turpentine to Soften
1 Part Plaster
Black Powder Color to Darken
Linseed Oil to Bind
Turpentine to Soften
Mix this thoroughly and work it firmly into the gaps with a brush, an old nailbrush or toothbrush would do well. Crumple a piece of newspaper into a ball and use it to scour the surfaces clean when you have finished with the grouting. Finish off by polishing with a soft cloth; you may need to wipe the glass over with a little turpentine for a perfect finish.
This concludes my hub on the basic techniques and principles of creating your own stained glass projects. I hope you have enjoyed learning the steps involved. Remember when starting any new craft that practice is always a good idea and start small. Once you gain confidence in your abilities, the possibilities become endless.
Thanks for stopping by & Happy Crafting!
No comments:
Post a Comment